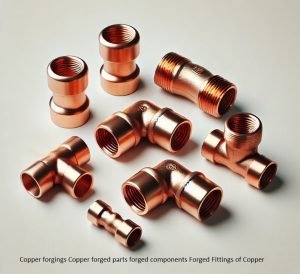
Copper Forging and Copper Forged Parts -Forged Components
Copper forging is a versatile manufacturing process that produces durable and precision-engineered components for various industries. By shaping copper alloys through hot forging or cold forging, the process enhances the material’s mechanical properties, strength, and performance. Copper’s exceptional conductivity, corrosion resistance, and malleability make it a preferred material for numerous applications, especially in the electrical sector. Conex is a leading producer of Copper Forgings, Copper forged parts and Copper forged Components from jamnagar, India.
Material Grades
We work with a variety of high-quality copper and copper alloy grades to suit diverse applications:
Grade | Description | Applications |
---|---|---|
C101 (Pure Copper) | Oxygen-free, high-conductivity copper with exceptional electrical properties. | Electrical and thermal applications. |
C110 (Electrolytic Tough Pitch) | Excellent conductivity and corrosion resistance. | Electrical wiring and connectors. |
C260 (Cartridge Brass) | High strength with good corrosion resistance. | Plumbing, industrial applications. |
C464 (Naval Brass) | Outstanding resistance to seawater and wear. | Marine and industrial applications. |
C655 (Silicon Bronze) | High strength and excellent weldability. | Architectural, marine hardware. |
C630 (Aluminum Bronze) | Superior wear resistance and mechanical strength. | Aerospace, heavy machinery. |
Properties of Copper Forged Components, Forged Parts
- High Electrical and Thermal Conductivity: Ideal for applications requiring efficient heat and electricity transfer.
- Corrosion Resistance: Excellent resistance to water, chemicals, and environmental degradation.
- Ductility and Malleability: Can be shaped into intricate designs without compromising strength.
- Wear Resistance: Perfect for applications with high mechanical stress and frequent motion.
- Aesthetic Appeal: Natural reddish-brown finish, suitable for architectural or decorative applications.
Industries That Use Copper Forgings
Copper forging serves diverse industries due to its unique properties:
- Electrical and Electronics:
- Switchgears, transformers, and power distribution systems.
- Automotive:
- Electrical terminals, heat exchangers, and fuel systems.
- Marine:
- Corrosion-resistant hardware for underwater and shipbuilding applications.
- Plumbing:
- Pipe fittings, valves, and connectors.
- Aerospace:
- High-strength, lightweight components for critical systems.
- Industrial Machinery:
- Bearings, bushings, and wear-resistant parts.
- Architectural:
- Decorative and structural elements such as brackets and hardware.
Copper Electrical Parts That Can Be Forged
- Bus Bars: High-conductivity copper bars used in power distribution systems.
- Electrical Terminals: Connectors for securing wires and cables in electrical circuits.
- Lugs: Tubular or flat terminals for cable connections in transformers and switchgears.
- Connectors: Precision-made components for joining electrical systems.
- Switchgear Components: High-strength, corrosion-resistant components for circuit breakers and panels.
- Transformer Parts: Grounding sockets, spade connectors, and brackets.
- Grounding Rods: Forged rods for safe electrical grounding in industrial and residential systems.
- Current-Carrying Components: Used in electrical motors and generators.
- Hotline Clamps: For live-line electrical maintenance.
- Copper Grounding clamps: for grounding and bonding/earthing accessories
- Forged Copper and Brass Transformer spades, Terminals, NEMA spacing spades, Spade Connectors, Transformer connectors in Copper, Brass and Bronze
- Contact Plates: Forged copper plates for industrial electrical contacts.
- Lightning Protection Components: Forged copper air terminals, clamps, and grounding connectors.
 Forged Copper Parts and Forged Copper components
- Electrical Components: Terminals, lugs, bus bars, and connectors.
- Plumbing Fittings: Elbows, tees, couplings, and flanges.
- Industrial Components: Bearings, bushings, and valve parts.
- Automotive Parts: Heat exchangers, brake system components, and fuel connectors.
- Marine Hardware: Propeller hubs, brackets, and anti-corrosion fittings.
Applications
- Electrical Systems: Power distribution, transformers, and switchgears.
- HVAC Systems: Refrigeration and air-conditioning systems.
- Automotive: Electrical systems and heat exchangers.
- Marine: Corrosion-resistant underwater hardware.
- Plumbing: Durable fittings for water distribution.
- Industrial Machinery: Wear-resistant components for heavy-duty applications.
Hot Forging vs. Cold Forging
Hot Forging
- Process: Copper is heated to a high temperature, making it malleable for shaping.
- Advantages:
- Allows for complex shapes and large components.
- Reduces material fractures.
- Improves mechanical properties through grain refinement.
- Applications: Large, intricate parts such as bus bars, connectors, and transformer components.
Cold Forging
- Process: Copper is forged at room temperature without heating.
- Advantages:
- Produces components with superior dimensional accuracy and surface finish.
- Retains the material’s inherent strength.
- Suitable for high-volume production.
- Applications: Small, precision parts like electrical terminals and fasteners.
Tolerances
- Typical Tolerances: ±0.1mm to ±0.5mm, depending on size and complexity.
- Post-Forging Machining: CNC machining can refine tolerances further to meet stringent requirements.
Why Choose Forged Copper Electrical Parts?
- Enhanced Conductivity: Ideal for power distribution and electrical systems.
- Durability: Exceptional strength and wear resistance.
- Customization: Tailored designs to meet specific industry needs.
- Cost-Effectiveness: Efficient material usage minimizes waste.
- Eco-Friendly: Fully recyclable material with minimal environmental impact.
Contact Us
At Conex, we specialize in producing high-quality forged copper components for the electrical and industrial sectors. Whether you require custom designs or standard parts, our expertise ensures precision, quality, and reliability.
Q & A for Copper Forging and Copper Forged Parts – Forged Components
Q1: What is Copper Forging, and why is it preferred for industrial applications?
A: Copper Forging is a manufacturing process where Copper or Copper Alloys are shaped under high pressure to form strong, durable forged components. It is preferred for industrial, electrical, marine, and automotive applications due to its high strength, excellent conductivity, superior corrosion resistance, and enhanced mechanical properties.
Q2: What are the benefits of using Copper Forged Parts over cast or machined components?
A: Copper Forged Parts offer numerous advantages over cast or machined components, including:
- Higher Strength and Durability – Improved grain structure enhances mechanical performance.
- Better Corrosion and Wear Resistance – Ideal for marine, electrical, and industrial environments.
- Superior Conductivity – Essential for electrical connectors, bus bars, and switchgear.
- Cost-Efficiency – Reduces material waste and improves production efficiency.
- Enhanced Machinability – Allows for complex geometries and tight tolerances.
Q3: What types of Copper Alloys are used in Forged Components?
A: Copper Forged Components can be made from various Copper Alloys, including:
- C101 (Oxygen-Free Copper) – Best for high-conductivity electrical applications.
- C110 (Electrolytic Tough Pitch Copper) – Commonly used in bus bars, grounding rods, and terminals.
- C182 (Chromium Copper) – High-strength, ideal for resistance welding electrodes.
- C464 (Naval Brass) – Excellent for marine and shipbuilding applications.
- C706 (Copper-Nickel Alloy) – Highly resistant to saltwater corrosion, used in marine fittings.
Q4: What are the different Copper Forging methods used for manufacturing?
A: Copper Forging processes include:
- Open Die Forging – Suitable for large, custom-shaped Copper Forged Parts.
- Closed Die Forging – Used for precision components with tight dimensional accuracy.
- Cold Forging – Produces high-strength, near-net-shape components with smooth surfaces.
- Hot Forging – Enhances the mechanical strength and toughness of Copper Forgings.
Q5: What are the key applications of Copper Forged Components?
A: Copper Forged Components are widely used in industries such as:
- Electrical & Power Transmission – Forged Copper Bus Bars, Switchgear Parts, Electrical Contacts.
- Automotive & Transportation – Battery Terminals, Heat Exchangers, Brake Components.
- Aerospace & Defense – Hydraulic Fittings, Valve Bodies, Actuator Components.
- Marine Industry – Corrosion-resistant Propeller Shafts, Flanges, Pipe Fittings.
- HVAC & Plumbing – Forged Copper Pipe Fittings, Manifolds, Connectors.
Q6: What tolerances can be achieved with Copper Forging?
A: Copper Forging allows for tight tolerances based on application requirements:
- Dimensional Tolerance: ±0.2mm to ±0.5mm for precision parts.
- Surface Finish: Ra 1.6 to Ra 3.2 µm depending on machining requirements.
- Bore & Hole Tolerances: H7 to H9 (ISO Standards) for high-precision applications.
Q7: How does Copper Forging enhance product longevity?
A: Copper Forging improves grain structure, mechanical strength, and impact resistance, making forged Copper parts more durable and wear-resistant. This ensures longer service life in demanding applications such as electrical power distribution, industrial machinery, and high-stress environments.
Q8: Can Copper Forged Parts be customized for specific applications?
A: Yes, custom Copper Forged Parts can be tailored to client specifications, including:
- Unique geometries and complex designs.
- Specific Copper Alloys based on industry requirements.
- Secondary operations like CNC machining, heat treatment, and coating.
- Surface finishes such as anodizing, polishing, and plating.
Q9: What surface finishes are available for Copper Forgings?
A: Copper Forgings can be finished with various treatments, including:
- Polished Finish – Enhances surface appearance and corrosion resistance.
- Nickel Plating – Provides additional protection for electrical components.
- Tin Coating – Used in electrical connectors to improve conductivity.
- Shot Blasting & Sandblasting – Removes surface imperfections and refines texture.
Q10: Where can I source high-quality Copper Forgings and Forged Parts?
A: We are a leading manufacturer and exporter of Copper Forgings, Forged Parts, and Forged Components, offering:
- Custom precision forgings in various Copper Alloys.
- High-strength, corrosion-resistant components for multiple industries.
- ISO-certified manufacturing processes ensuring quality and reliability.
- Competitive pricing and global shipping with flexible production capabilities.
Â
🔹 Request a Quote – Get a customized price for your Copper Forging needs.
📧 Email Us – Ask for a product catalog or technical details.
📞 Contact Us – Reach out via Phone or WhatsApp for quick assistance.